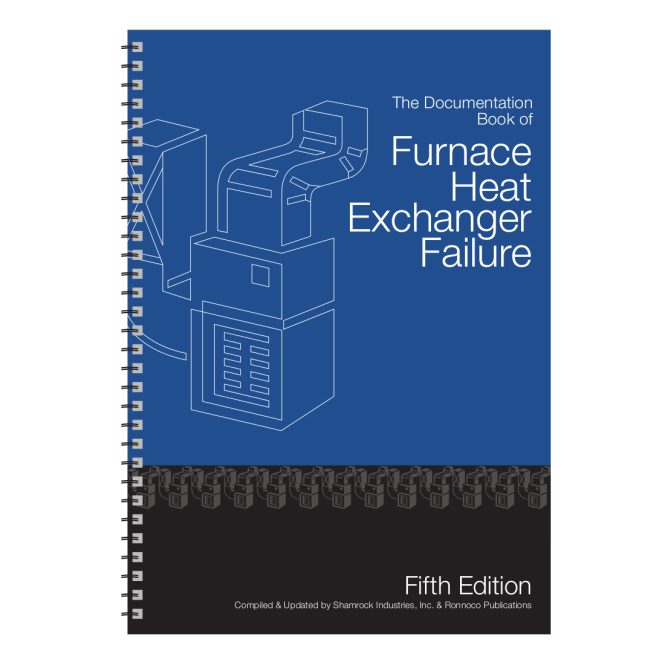
Heat exchanger failures can lead to significant operational disruptions, safety risks, and substantial economic losses. Understanding the potential dangers and implementing preventative measures is critical for maintaining efficient and safe operations. A heat exchanger is a device that transfers heat between two fluids without mixing them. They are ubiquitous in industrial settings, and understanding their function and potential failure points is crucial for effective maintenance and repair. This comprehensive guide explores the various causes, dangers, and repair methods for heat exchanger failures, aiming to equip readers with the knowledge and strategies for minimizing downtime and safety risks. We will explore the different types of heat exchangers and the common failure modes. Then, we will delve into preventive maintenance strategies and explore various repair methods. Finally, we will look at case studies of heat exchanger failures and how they were resolved.
Understanding Heat Exchanger Failures: Types and Causes
Different Types of Heat Exchangers
Heat exchangers come in various designs, each with its specific operating characteristics and potential failure points. Common types include shell-and-tube, plate, and fin-tube heat exchangers. Understanding the specific design of a heat exchanger is crucial for identifying potential failure modes. Each type has varying susceptibility to certain failure mechanisms.
Common Causes of Failure
Several factors contribute to heat exchanger failures, including corrosion, fouling, material fatigue, and improper operation. Corrosion, the gradual deterioration of the material due to chemical reactions, is a significant cause. Fouling, the build-up of deposits on the heat transfer surfaces, can impede heat transfer, potentially leading to overheating and failure. Material fatigue, resulting from repeated stress cycles, can lead to cracks or fractures. Additionally, improper operation, such as exceeding design parameters or inadequate maintenance, contributes to failures.
Evaluating Potential Dangers
Safety Hazards Associated with Failures
Heat exchanger failures can result in a cascade of hazardous conditions, including burns, chemical releases, and explosions, if not addressed properly. It’s crucial to understand the hazards associated with specific types of heat exchangers, as different fluids and temperatures pose different risks. Safety protocols and emergency procedures should be readily available.
Mitigation Strategies
Implementing proactive safety measures is crucial to prevent accidents. Regular inspections and maintenance schedules are essential. These inspections should identify any potential issues like leaks or corrosion. Emergency response plans, including procedures for handling spills and chemical releases, should be in place.
Repair Methods and Strategies
Repair Techniques
Various repair strategies are available for heat exchanger failures, including cleaning, patching, replacement of parts, and complete replacement. Choosing the appropriate repair method depends on the severity of the damage and the type of heat exchanger. A leak, for instance, might be addressed with a patch, while a significant structural damage requires full replacement.
Repair Cost Considerations
The cost of repair can vary significantly, depending on the extent of the damage, the complexity of the repair, and the availability of spare parts. Preventive maintenance can reduce repair costs by catching issues early, while major repairs can be significantly more expensive. Assessing the repair cost versus potential risks is crucial to justify replacement decisions and prevent costly damages.
Preventive Maintenance Strategies
Regular Inspection Schedules
Establishing a routine inspection schedule is vital for identifying potential problems before they escalate into major failures. Regular visual inspections, as well as non-destructive testing methods, can aid in early detection of corrosion, leaks, and other damage. A well-structured maintenance plan is essential for proactive maintenance.
Implementing Proper Cleaning Procedures
Implementing thorough cleaning procedures is vital to prevent fouling and ensure optimal heat transfer efficiency. Fouling can reduce the heat transfer capability of the heat exchanger and result in overheating or other operational inefficiencies. Proper cleaning methods must be employed for every type of heat exchanger to avoid damage during cleaning.
Case Studies and Real-World Examples
Case Study 1: Fouling Issues
A recent case study in a chemical plant highlighted the consequences of inadequate cleaning procedures. Fouling buildup reduced heat transfer, leading to equipment overheating and potential catastrophic failure. The incident highlighted the importance of regular cleaning and maintenance to prevent these issues.
Case Study 2: Corrosion Issues
Another case study demonstrated the long-term effects of corrosion in a power plant. Corrosion on the heat exchanger caused gradual degradation of the material, leading to leaks and eventual replacement of the heat exchanger. This underscores the importance of regular corrosion checks and timely maintenance.
Frequently Asked Questions
What are the key indicators of potential heat exchanger failure?
Key indicators of potential heat exchanger failure include leaks, unusual noise, changes in performance, and visible damage. Regular visual inspections and monitoring of operating parameters can help identify issues early. For example, reduced efficiency or unexpected temperature fluctuations can signal a problem, requiring investigation and potential repair. Prompt attention to these signs is critical in preventing more significant issues.
What are the long-term consequences of neglecting heat exchanger maintenance?
Neglecting heat exchanger maintenance can lead to serious long-term consequences. These include costly repairs, safety risks, increased energy consumption due to reduced efficiency, potential environmental damage, and possible downtime in production, which can lead to a loss in productivity and profit. Failure to take necessary maintenance measures can have significant consequences.
In conclusion, heat exchanger failures pose significant risks, requiring careful inspection, timely maintenance, and adherence to safety protocols. Understanding the causes of failure, implementing preventive measures, and executing effective repair strategies are crucial for maintaining operational safety and minimizing potential hazards. By addressing potential issues proactively, industries can prevent costly downtime and safeguard personnel. For a more in-depth analysis and to explore advanced troubleshooting techniques, consider consulting reputable engineering resources and industry experts for optimal results.